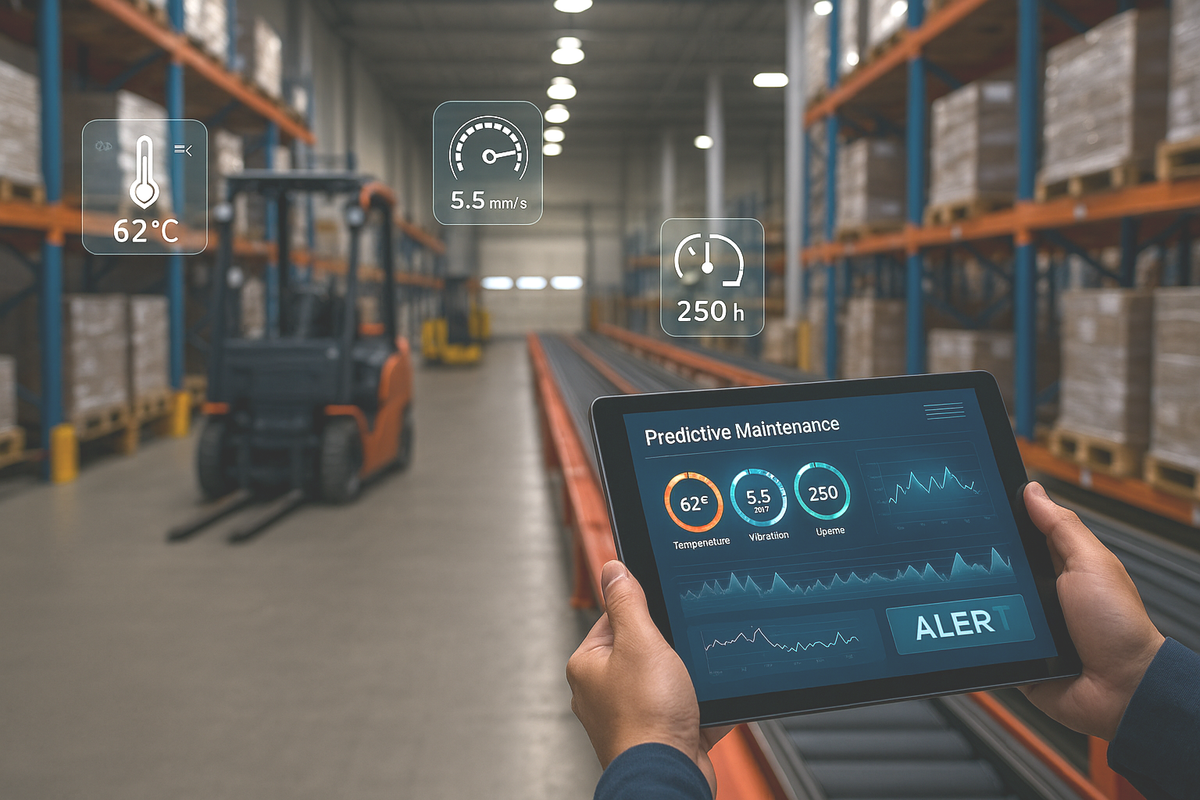
By Robert Skinner | WBN News | May 15, 2025
Subscribe To WBN News: https://wbn.digital?fpr=robert10
In the high-stakes environment of Tilbury Industrial Park, equipment downtime can cost businesses thousands of dollars per hour. That’s why a growing number of South Delta warehouses and logistics firms are exploring AI-powered predictive maintenance to keep operations running smoothly — and profitably.
Predictive maintenance uses machine learning algorithms and sensor data to anticipate failures before they happen. Rather than waiting for machines to break down, these systems monitor vibration, temperature, and usage patterns in real-time to detect anomalies and recommend service — long before an issue shuts down a conveyor, forklift, or HVAC system.
From Reactive to Proactive
Traditionally, maintenance has been either reactive (fix it when it breaks) or scheduled (fix it at set intervals). But both approaches are flawed — either you lose time and money due to unexpected failures or waste resources servicing equipment that’s still in peak condition.
With predictive AI tools like Uptake, SparkCognition, or Seebo, Tilbury-based firms can now:
- Minimize unexpected downtime
- Extend the life of critical equipment
- Reduce manual inspections and unnecessary part replacements
- Improve scheduling for technicians and resources
“We’ve cut unscheduled downtime by 40%,” says a warehouse operations lead at a logistics firm near River Road. “The system notifies us days before anything major fails.”
Local Integration in Action
While large-scale plants across North America have embraced predictive maintenance, South Delta firms are now catching up — especially as cloud-based platforms become more affordable.
Several Tilbury warehouses have begun outfitting key systems with vibration sensors and using AI dashboards to alert supervisors of maintenance needs. These setups can often be installed without replacing existing machines, using edge devices and wireless IoT connections.
The Bottom Line
AI-powered maintenance doesn't just prevent breakdowns — it shifts your entire operation from firefighting to strategic planning. For the Tilbury Industrial sector, it’s a competitive edge hiding in plain sight.
What’s Next in the Series
🔍 Coming up next: “AI in Energy Management: Reducing Utility Costs and Carbon Emissions in South Delta’s Industrial Sector”
We’ll explore how warehouses and facilities are using AI to manage energy usage more efficiently — and lower operating costs at the same time.
Robert is an experienced "AI Assisted" business systems developer and coach.
Give him a call at +1 604-220-4750 or connect on LinkedIn: https://www.linkedin.com/in/rlskinner/
WBN News - South Delta Edition
Robert Skinner - Publisher
#WBN News - South Delta #Robert Skinner - Publisher #Tilbury Industrial #AI Maintenance #South Delta Industry #Smart Warehousing #Delta BC Tech