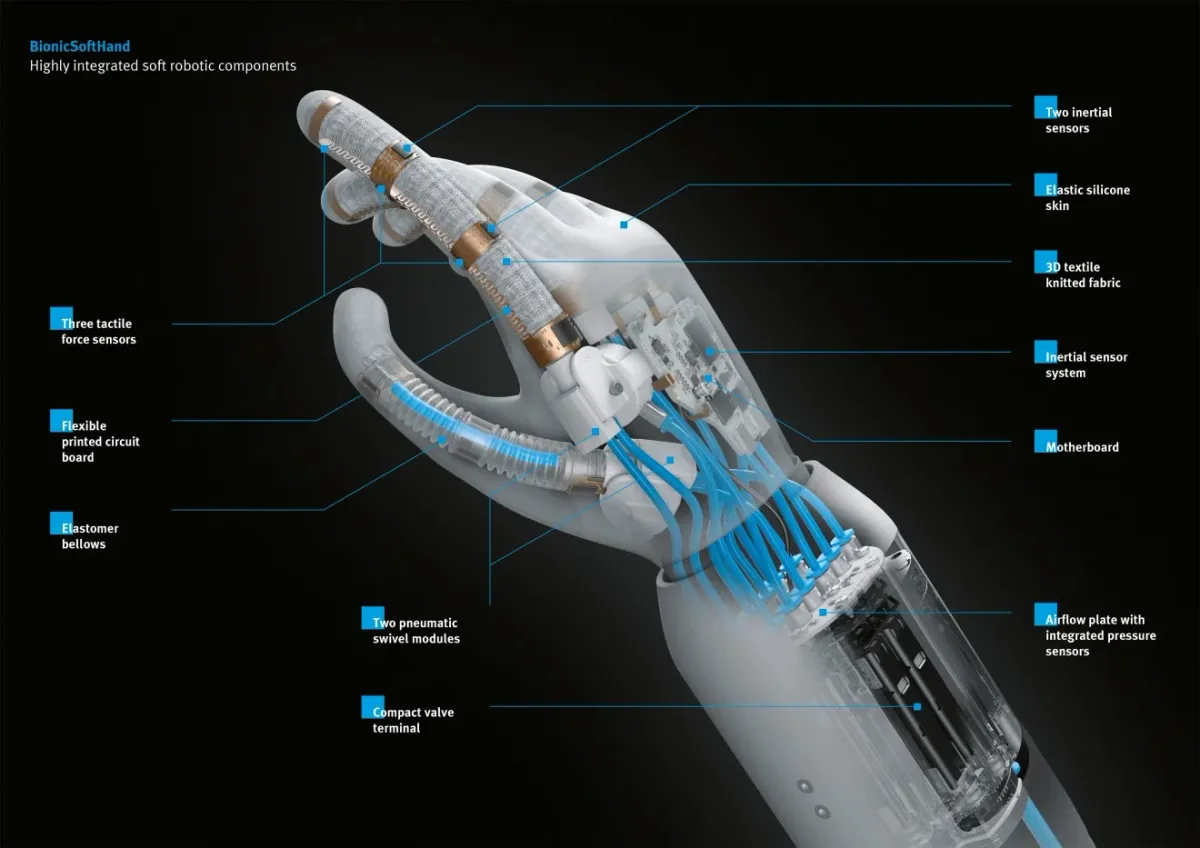
By Elke Porter | Canadian German News | May 21, 2025
Subscription to WBN and being a Contributor is FREE!
In Zurich, a groundbreaking team of engineers and scientists at the Bionic Learning Network is transforming the way robots interact with the world by drawing inspiration directly from nature. Through a fusion of biology, artificial intelligence, and pneumatic engineering, they have developed bionic grippers and soft robotic systems that mimic the grace, adaptability, and efficiency of living organisms.
One of the most remarkable innovations to emerge is the BionicSoftHand, a pneumatic robot hand capable of performing complex tasks like gripping, rotating, or typing—actions we take for granted but are astonishingly complex for machines. Modeled after the human hand, the BionicSoftHand not only replicates its structure but also its learning behavior. Using reinforcement learning, the robotic hand doesn’t mimic specific motions—instead, it is given goals and learns through trial and error, improving its performance with every interaction.
A major breakthrough in this learning process comes from the use of a digital twin—a virtual simulation of the robot hand. This allows developers to train the hand in a parallel digital environment using data from depth-sensing cameras and AI algorithms. With massively parallel learning, virtual hands share knowledge across all models, significantly speeding up the learning curve. Once trained, the learned strategies are transferred to the physical BionicSoftHand for real-world application.
Unlike traditional robotic hands with motors or cables, the BionicSoftHand is made of pneumatic bellows encased in a 3D-knitted textile fabric, offering twelve degrees of freedom. Its flexible and bone-free structure bends when air fills the chambers and remains extended when emptied, with additional swivel modules allowing lateral movement of the thumb and index finger. These features grant the robot a level of dexterity and safety ideal for working alongside humans.
Engineered for efficiency, the hand uses compact piezo-controlled valves to reduce tubing complexity, allowing quick integration into existing robotic systems. When paired with Festo’s BionicCobot or BionicSoftArm, the BionicSoftHand becomes part of a new generation of soft robots capable of collaborating directly with humans in shared workspaces.
With its natural movement, smart learning capability, and safe, modular design, the Zurich-born BionicSoftHand is paving the way for the future of human–robot interaction—where machines learn, adapt, and support with the sensitivity and skill once exclusive to living beings.
#Bionic Soft Hand #Soft Robotics #Human Robot Collaboration #AI Innovation #Zurich Tech #Future Of Work #WBN News Vancouver #Elke Porter
Connect with Elke at Westcoast German Media or on LinkedIn: Elke Porter or contact her on WhatsApp: +1 604 828 8788